Introduction
Preventive maintenance is the cornerstone of reliable and efficient operation for Ariel engine compressors. These critical pieces of industrial equipment play a vital role in natural gas processing, oil and gas transportation, and various industrial applications. A well-designed maintenance strategy can significantly extend equipment life, reduce unexpected downtime, and optimize overall operational performance.
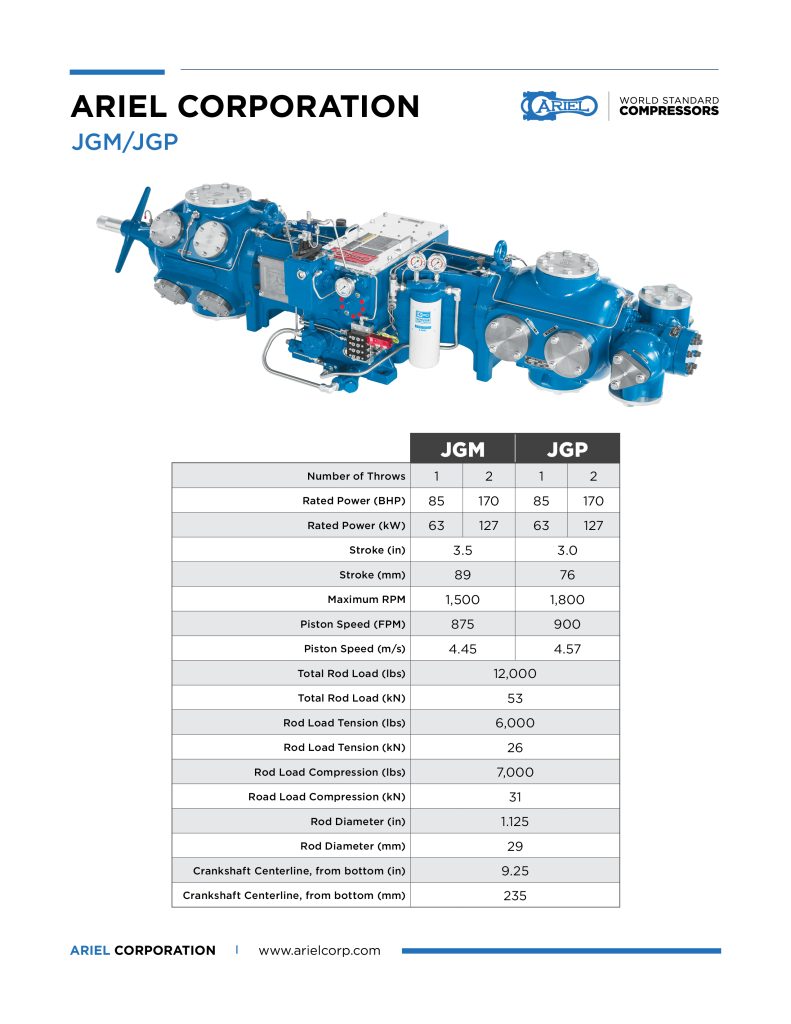
Understanding Ariel Compressor Systems
System Components
Ariel compressors typically consist of several key components:
- Compressor frame
- Cylinders and pistons
- Crankshaft and connecting rods
- Valves and valve assemblies
- Lubrication system
- Cooling system
- Control and monitoring systems
Importance of Preventive Maintenance
Effective preventive maintenance addresses:
- Equipment reliability
- Safety compliance
- Performance optimization
- Cost management
- Extended equipment lifecycle
Comprehensive Maintenance Strategy
1. Routine Inspection Protocols
Daily Inspections
- Visual equipment assessment
- Lubricant level checks
- Operational temperature monitoring
- Vibration and noise analysis
- Seal and gasket integrity examination
Weekly Inspections
- Detailed lubrication system evaluation
- Cooling system performance review
- Control system diagnostic checks
- Compression cylinder condition assessment
- Valve operation verification
Monthly Inspections
- Comprehensive alignment checks
- Bearing condition assessment
- Compression ratio verification
- Electrical system comprehensive review
- Filtration system thorough examination
2. Lubrication Management
Oil Analysis Program
- Quarterly oil sampling
- Comprehensive fluid analysis
- Contamination detection
- Wear metal analysis
- Viscosity and additive package evaluation
Lubrication Best Practices
- Use manufacturer-recommended lubricants
- Maintain proper oil cleanliness
- Monitor oil temperature and pressure
- Implement systematic oil change intervals
- Track oil consumption and degradation
3. Mechanical Component Maintenance
Cylinder Maintenance
- Periodic cylinder liner inspection
- Piston ring condition assessment
- Cylinder head bolt torque verification
- Wear pattern analysis
- Honing and surface treatment as required
Valve Assembly Care
- Regular valve plate inspection
- Spring tension verification
- Valve seat condition assessment
- Replacement of worn components
- Precise valve clearance adjustments
Crankshaft and Bearings
- Vibration analysis
- Bearing clearance measurement
- Surface condition evaluation
- Alignment precision checks
- Lubrication system effectiveness review
4. Cooling System Management
Heat Exchanger Maintenance
- Regular cleaning protocols
- Tube bundle integrity checks
- Coolant quality monitoring
- Corrosion prevention strategies
- Performance efficiency testing
Cooling Medium Management
- Water treatment programs
- Chemical composition analysis
- Biological growth prevention
- Pressure and flow rate monitoring
- Temperature differential assessment
5. Electrical and Control Systems
Electrical Component Care
- Insulation resistance testing
- Connection point torque verification
- Protective relay calibration
- Power supply stability assessment
- Electrical system diagnostics
Control System Maintenance
- Sensor calibration
- Software update management
- Communication interface checks
- Programmable logic controller (PLC) diagnostics
- Cybersecurity vulnerability assessment
6. Performance Monitoring Technologies
Predictive Maintenance Techniques
- Vibration analysis
- Thermographic imaging
- Acoustic emission monitoring
- Lubricant spectroscopic analysis
- Performance trend tracking
Data-Driven Maintenance Approach
- Implement condition monitoring systems
- Develop performance baseline
- Create alert and intervention thresholds
- Utilize machine learning predictive algorithms
- Integrate IoT sensor networks
Maintenance Documentation and Record Keeping
Comprehensive Maintenance Logs
- Detailed service history
- Component replacement tracking
- Performance trend documentation
- Inspection result archives
- Recommended future interventions
Compliance and Safety Documentation
- Regulatory standard adherence
- Equipment certification maintenance
- Safety system verification
- Risk assessment documentation
- Environmental compliance records
Economic Considerations
Maintenance Cost Management
- Develop preventive maintenance budget
- Calculate return on maintenance investment
- Minimize unexpected downtime costs
- Optimize spare parts inventory
- Implement strategic maintenance scheduling
Long-Term Asset Management
- Lifecycle cost analysis
- Equipment replacement planning
- Performance degradation tracking
- Technological upgrade evaluation
- Reliability-centered maintenance strategies
Conclusion
Implementing a comprehensive preventive maintenance strategy for Ariel engine compressors requires a systematic, data-driven approach. By integrating routine inspections, advanced monitoring technologies, and proactive maintenance techniques, operators can achieve:
- Maximum equipment reliability
- Optimized operational performance
- Reduced lifecycle costs
- Enhanced safety compliance
- Sustainable industrial operations
Continuous improvement and adaptation of maintenance protocols remain critical in managing these complex mechanical systems effectively.
Recommended Maintenance Schedule
Interval | Primary Focus | Key Activities | |
Daily | Operational Readiness | Visual checks, lubrication levels, temperature monitoring | |
Weekly | System Performance | Detailed system evaluations, diagnostic checks | |
Montly | Comprehensive Assessment | Alignment, bearing condition, compression ratio verification | |
Quarterly | Predictive Maintenance | Oil analysis, vibration monitoring, advanced diagnostics | |
Annualy | Major Service | Complete system overhaul, comprehensive replacements |
Maintenance Schedule Overview
Daily Maintenance Checklist
- Visual Inspection
- Check for external leaks
- Inspect mechanical condition
- Verify lubricant levels
- Monitor operating temperatures
- Check vibration and noise levels
- Operational Checks
- Verify control system functionality
- Assess instrument readings
- Confirm proper startup and shutdown procedures
- Evaluate seal and gasket integrity
Weekly Maintenance Tasks
- Lubrication System
- Comprehensive oil analysis
- Check oil quality and contamination
- Verify oil filter condition
- Assess lubricant viscosity
- Evaluate cooling system performance
- Mechanical Components
- Cylinder liner inspection
- Piston ring condition assessment
- Valve plate and spring examination
- Compression ratio verification
- Bearing clearance measurement
Monthly Maintenance Procedures
- Detailed System Assessment
- Comprehensive alignment checks
- Vibration analysis
- Thermographic imaging
- Electrical system diagnostics
- Control system calibration
- Advanced Inspections
- Crankshaft condition evaluation
- Compression cylinder detailed examination
- Valve assembly thorough review
- Cooling system performance testing
- Protective device functionality verification
Quarterly Maintenance Protocol
- Advanced Diagnostic Procedures
- Comprehensive oil spectroscopic analysis
- Wear metal detection
- Fluid contamination assessment
- Predictive maintenance technology application
- Performance trend tracking
- Critical Component Evaluation
- Detailed bearing assessment
- Comprehensive valve system analysis
- Cylinder performance verification
- Cooling system efficiency testing
- Electrical system comprehensive review
Annual Major Service
- Complete System Overhaul
- Full component inspection and potential replacement
- Complete system disassembly
- Precision measurements and alignments
- Comprehensive parts replacement
- Advanced diagnostic testing
- Major Component Replacement
- Crankshaft detailed evaluation
- Cylinder liner potential replacement
- Valve assemblies comprehensive review
- Bearing system complete assessment
- Control system firmware updates
Maintenance Intervention Criteria
Performance Degradation Indicators
- Increased vibration levels
- Abnormal temperature variations
- Compression efficiency reduction
- Lubricant quality deterioration
- Unusual noise or operational characteristics
Immediate Intervention Requirements
- Significant performance deviation
- Critical component wear
- Safety system malfunction
- Unexpected operational interruptions
- Environmental compliance issues
Maintenance Documentation
Comprehensive Record Keeping
- Detailed service history documentation
- Component replacement tracking
- Performance trend analysis
- Inspection result archiving
- Predictive maintenance data management
Economic Considerations
Maintenance Cost Optimization
- Develop preventive maintenance budget
- Calculate maintenance investment returns
- Minimize unexpected downtime
- Optimize spare parts inventory
- Strategic maintenance scheduling