Gas system integration might sound like a fancy technical term, but it’s actually about making sure all the different parts of a gas system work together in harmony. Imagine a huge orchestra where each instrument has to play in tune with the others to create beautiful music. That’s what gas system integration does for various industries that rely on gas, whether it’s for energy, manufacturing, or even transportation.
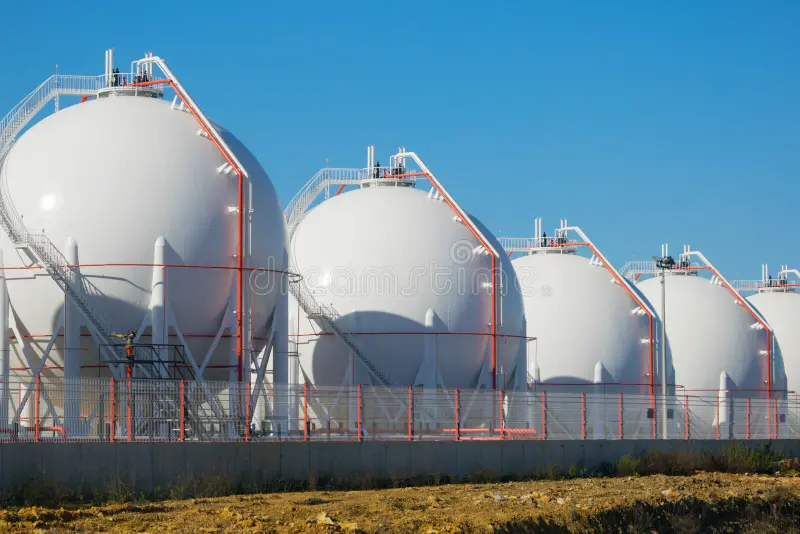
So, how does it work? And why is it so important? Let’s break it down, keep it simple, and explore the basics of gas system integration.
What is Gas System Integration?
At its core, gas system integration is about linking all the pieces of a gas system so that they function efficiently and without hiccups. It involves connecting different components like compressors, pipelines, valves, gas treatment units, and storage facilities, ensuring they work together in a way that optimizes gas production, transportation, and consumption.
Imagine you’re running a big factory that uses natural gas for power. You’ve got to make sure that gas flows smoothly from the pipeline into the compressors, then through the treatment process, and eventually to where it’s used in the factory’s machines. Without proper integration, one misstep could result in a shutdown, inefficiency, or worse, a safety hazard.
Why is Gas System Integration Important?
Gas systems are complicated. They involve high pressures, a lot of moving parts, and the need for precise control to ensure safety and efficiency. When all these components are properly integrated, you get:
- Increased Efficiency: If the system components aren’t integrated properly, there could be waste, delays, or energy losses. Integration ensures that gas flows smoothly and without interruption, making the system as energy-efficient as possible.
- Cost Savings: Efficient integration can help minimize unnecessary costs, whether that’s in energy consumption, maintenance, or repairs. When the system works well, you spend less on fixes or upgrades.
- Safety: Gas systems handle flammable materials, so safety is a huge priority. Poor integration can lead to leaks, explosions, or other accidents. By integrating systems correctly, you ensure that each component is working in sync, reducing risks.
- Scalability: As companies grow or need more gas, the integrated system can be scaled up more easily. With proper integration, you can expand capacity or connect new systems without disrupting the whole setup.
- Environmental Benefits: A well-integrated gas system can reduce emissions by optimizing the processes and minimizing waste. It also ensures better monitoring and compliance with environmental regulations.
Key Components in Gas System Integration
To understand how integration works, let’s first take a look at the core components that make up a typical gas system.
- Gas Compressors: These are the heart of the system. Compressors are used to increase the pressure of the gas so it can travel long distances through pipelines. There are different types of compressors—reciprocating, centrifugal, and rotary screw—but the goal is always the same: to increase pressure and maintain a consistent flow.
- Gas Pipelines: Pipelines are the channels through which gas flows. Once compressed, the gas travels through these pipelines to get from the production site to consumers, whether it’s factories, homes, or power plants. The pipes must be sturdy and capable of handling high-pressure gas.
- Valves and Regulators: These control the flow of gas throughout the system. Valves help regulate pressure and prevent surges that could damage the equipment. Regulators ensure that the gas is delivered at the right pressure for use.
- Gas Treatment Units: Natural gas often contains impurities like sulfur, carbon dioxide, and water. Treatment units clean the gas before it’s used or transported, ensuring it meets the required quality standards.
- Storage Facilities: These are where gas is stored, usually in large tanks or underground reservoirs. Having a good storage system is important for maintaining a steady supply, especially when demand fluctuates.
- Monitoring and Control Systems: These systems keep track of how the gas is flowing, whether pressure levels are stable, and if any part of the system is malfunctioning. They provide real-time data to operators, so they can respond to issues before they become bigger problems.
How Gas System Integration Works
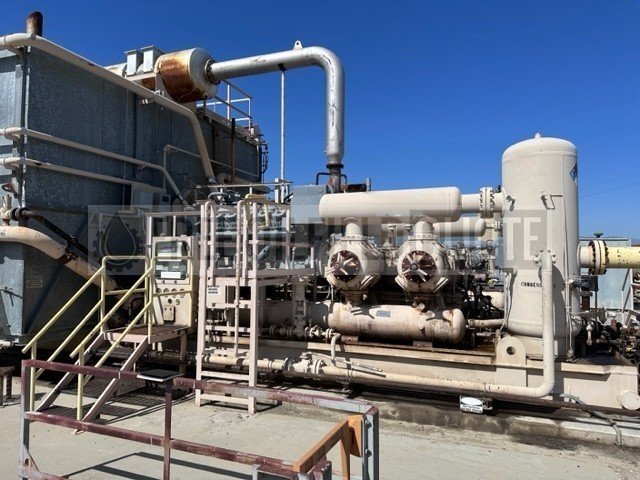
Now that we know what the key components are, let’s talk about how integration happens.
- Planning and Design: The first step in integrating a gas system is planning. This involves determining how all the parts will connect, how the gas will flow, and what kind of equipment is needed. It’s kind of like putting together a puzzle—each piece has to fit just right for everything to work smoothly.
- Connecting the Dots: Once the design is in place, the next step is physically installing and connecting all the components. This could mean laying down pipelines, installing compressors, and setting up treatment units. At this stage, the gas system is taking shape, but it’s not fully functional until everything is properly wired up.
- System Optimization: After everything is installed, it’s time to fine-tune the system for optimal performance. This could involve adjusting the pressure in the pipelines, calibrating the compressors, or making sure the valves open and close at the right times. This step is crucial because even small adjustments can lead to huge improvements in efficiency.
- Automation and Control: Gas systems today are often controlled by automated systems that monitor everything in real time. This allows operators to keep an eye on the system from afar and respond quickly to any issues. For example, if a gas leak is detected, the system can automatically shut down certain valves or compressors to prevent a bigger problem.
- Regular Maintenance: Once the system is up and running, it requires regular maintenance to keep everything working smoothly. This could involve checking for leaks, replacing worn-out parts, or recalibrating equipment. With good maintenance, a gas system can run for years with minimal downtime.
The Challenges of Gas System Integration
Even though gas system integration offers a lot of benefits, it’s not without its challenges. Here are a few hurdles that companies face when trying to integrate gas systems:
- Complexity: Gas systems are inherently complex. Different technologies, standards, and regulations must be considered, and integrating them all can be tricky. For example, you might have to combine old systems with newer ones, which could require custom solutions.
- Cost: Building and maintaining a gas system is expensive. Not only do you need to invest in the physical infrastructure, but you also need to have specialized staff who can manage and troubleshoot the system. However, the upfront costs often pay off in the long run with improved efficiency and reduced maintenance.
- Safety Concerns: Gas systems are high-risk environments. Poor integration can lead to leaks, explosions, or environmental damage. Ensuring that all components work together without compromising safety is a huge challenge for engineers.
- Environmental Impact: While gas systems are necessary for many industries, they also come with environmental concerns. Integrating cleaner technologies and improving efficiency can help reduce the carbon footprint, but it’s still an ongoing challenge to minimize the environmental impact of gas systems.
- Regulations: Gas systems are highly regulated to ensure safety and environmental protection. Staying compliant with regulations can be difficult, especially when integrating new technologies or expanding existing systems. This requires constant monitoring and sometimes redesigning certain parts of the system to meet the latest standards.
The Future of Gas System Integration
As the world moves toward more sustainable energy solutions, gas systems will continue to evolve. Gas system integration will play a key role in ensuring that these systems are not only efficient and safe but also environmentally friendly. Here are a few trends to watch:
- Smart Gas Systems: With the rise of IoT (Internet of Things) technology, gas systems are becoming smarter. Sensors and monitoring devices can track gas flow, pressure, and leaks in real time, sending alerts to operators who can respond faster. This makes the system more efficient and safer.
- Integration with Renewable Energy: As we move toward renewable energy sources like wind and solar, integrating gas systems with these technologies will become increasingly important. Gas can be used as a backup power source when renewable energy isn’t available, helping to create a more resilient energy grid.
- Green Technologies: Green technologies, such as carbon capture and storage (CCS), will become more integrated into gas systems. These technologies help capture carbon dioxide emissions from natural gas and prevent them from entering the atmosphere, reducing the environmental impact of gas systems.
- Automation and AI: The future of gas system integration will likely involve more automation and artificial intelligence. AI can optimize gas flow, detect problems, and even predict future maintenance needs, making gas systems more efficient and reliable.
Conclusion
Gas system integration is all about making sure everything works together seamlessly, from compressors and pipelines to treatment units and storage facilities. It’s a crucial part of industries that rely on gas for power, manufacturing, and transportation. Proper integration leads to improved efficiency, cost savings, safety, and even environmental benefits. But, like anything complex, it comes with its challenges—complexity, cost, safety concerns, and regulations.
In the future, gas systems will become even smarter and more efficient, thanks to advancements in technology like IoT, AI, and green innovations. As we continue to integrate more renewable energy sources and tackle environmental concerns, gas system integration will be key to ensuring that our energy systems are reliable, sustainable, and safe.
Whether you’re working in the gas industry or just curious about how gas systems function, understanding the basics of gas system integration gives you a better appreciation for the complexity and importance of these systems. It’s all about connecting the dots and making sure the gas flows as it should—efficiently, safely, and without interruption.
Case Studies: Real-Life Examples of Gas System Integration
To help illustrate how gas system integration works in practice, let’s take a look at a couple of real-world examples. These case studies will show how industries are applying these concepts to improve their operations and maintain efficiency.
Case Study 1: Natural Gas Transmission Systems
In many countries, natural gas is transported over long distances via pipelines. For example, in the United States, the Transcontinental Gas Pipe Line (Transco) system operates as one of the largest natural gas pipeline networks in the country. This vast network moves gas from production areas in the Gulf of Mexico to major metropolitan areas on the East Coast.
When it comes to integrating such a large-scale gas system, the complexity increases exponentially. The system needs to account for a range of pressures, temperatures, and possible gas treatments. Transco has adopted advanced automation systems to monitor pressure levels, flow rates, and safety measures in real-time, helping operators identify potential issues before they become major problems. By integrating automated control systems, they ensure smooth operations, improve gas delivery reliability, and even anticipate demand fluctuations.
Additionally, compressor stations are strategically located along the pipeline to maintain the pressure of the gas as it travels. These stations are interconnected and monitored by a central control system, ensuring that they are all functioning in unison. Without proper integration, issues such as pressure drops or flow interruptions could occur, leading to delays or costly repairs.
Case Study 2: Gas Systems in Power Plants
Another key example is the use of integrated gas systems in natural gas power plants. A modern gas power plant, such as the Kwinana Power Station in Australia, uses a highly integrated gas system for the production of electricity. Gas turbines generate electricity by burning natural gas, and the integration of gas compression, combustion, and exhaust systems is essential for optimal performance.
Here’s how integration plays a role:
- Gas Supply and Compression: Natural gas is compressed and delivered to the turbines at the right pressure and temperature. Compressors help optimize gas delivery, making sure that the turbines get a consistent supply of fuel.
- Turbine Operation: The compressed gas enters the combustion chamber, where it is ignited and converted into high-speed exhaust gases. These gases drive turbines that generate electricity.
- Waste Heat Recovery: One of the best ways to boost efficiency is by integrating a combined cycle system. The exhaust gases from the turbines are used to generate steam in a heat recovery steam generator (HRSG), which powers a steam turbine to generate additional electricity.
This type of integration maximizes efficiency, reducing fuel costs, and boosting the overall power output of the plant. The seamless connection between gas supply, turbine operation, and waste heat recovery not only ensures that energy production is efficient, but it also minimizes the environmental impact by reducing emissions.
Case Study 3: Oil and Gas Refineries
In oil and gas refineries, the integration of gas systems is vital for maintaining product quality and process safety. Refining crude oil into products like gasoline, diesel, and jet fuel requires careful control of pressure, temperature, and gas flow rates throughout various parts of the facility.
Refineries often rely on integrated systems that monitor flaring systems, heat exchangers, and gas recovery units. Flaring is a safety measure that involves burning off excess gas to prevent it from building up to dangerous levels. Proper integration ensures that gas flaring is minimized and that recovered gases are reused within the refinery or sent to pipelines.
A good example of integrated gas systems in refineries can be seen at the ExxonMobil Refinery in Baton Rouge, Louisiana, one of the largest refineries in the U.S. The facility uses advanced monitoring systems to detect any fluctuations in pressure or temperature that could indicate a problem with gas flow. Automation systems help regulate the use of natural gas throughout the refinery, making sure that it’s always supplied to the right areas at the right time.
The Role of Renewable Energy in Gas System Integration
As the world shifts toward cleaner, greener energy sources, gas systems are increasingly being integrated with renewable energy sources like solar and wind. This hybrid approach is crucial for reducing carbon emissions while maintaining a reliable energy supply.
Gas as a Backup for Renewables
Renewable energy, like solar and wind, is intermittent—it’s not always available when we need it. Solar power works during the day, and wind energy depends on wind conditions. This is where natural gas comes in. Gas-fired power plants are used as backup sources to maintain energy supply during times when renewable sources are unavailable.
Integration of these two energy systems can be tricky, though. Gas plants need to be ready to ramp up production quickly when renewable energy generation falls, requiring advanced control systems. This integration is sometimes called “grid balancing,” and it ensures a steady power supply without relying too heavily on fossil fuels.
Green Gas Technologies
In addition to this backup role, the integration of green technologies within gas systems is also becoming more common. One example is the use of biogas—gas that is produced through the decomposition of organic waste. By integrating biogas production with natural gas systems, companies can reduce their reliance on fossil fuels and use cleaner energy sources.
For example, some cities are now implementing biogas-to-grid systems, where biogas generated from landfills, agricultural waste, or sewage is converted into natural gas and fed into existing pipelines. This integration allows cities to use renewable energy without having to build entirely new infrastructure.
Another innovative development is carbon capture and storage (CCS), where carbon dioxide produced from natural gas power plants is captured and stored underground instead of being released into the atmosphere. Integrating CCS into gas systems helps reduce the environmental impact of gas usage.
Future Innovations in Gas System Integration
The future of gas system integration looks bright, with plenty of exciting innovations on the horizon. Let’s explore a few of the key trends that could shape the next generation of gas systems.
1. Digitalization and the Internet of Things (IoT)
One of the most significant advances in gas system integration is the rise of IoT (Internet of Things) technology. Sensors, connected devices, and real-time monitoring systems are becoming integral to modern gas systems. These devices allow for continuous monitoring of pressure, flow rates, and gas quality, helping operators make data-driven decisions.
IoT integration can also enable predictive maintenance. Instead of waiting for equipment to break down, operators can use data to predict when parts will need replacing, avoiding unnecessary downtime and preventing costly repairs.
2. Advanced AI and Machine Learning
Artificial intelligence (AI) and machine learning are increasingly being used to optimize gas system operations. These technologies can analyze vast amounts of data collected from gas systems to predict demand, optimize energy flow, and identify potential issues before they occur. For instance, machine learning algorithms could analyze the data from sensors in real-time, adjusting compressor settings or predicting when maintenance is required.
3. Microgrids and Distributed Energy Systems
Microgrids are small, localized energy systems that can operate independently from the main grid. These systems often combine multiple energy sources—renewable energy, natural gas, and even battery storage—to provide a stable energy supply. The integration of gas systems into microgrids allows for more flexibility and resilience, especially in remote areas or places with unreliable power grids.
4. Hydrogen Integration
Hydrogen is often seen as the fuel of the future, and it can be integrated into existing gas systems to replace natural gas. Hydrogen can be produced through various methods, including electrolysis (using renewable electricity to split water into hydrogen and oxygen). As hydrogen technology improves, we may see more hydrogen-powered gas turbines or blended hydrogen-natural gas systems.
Conclusion
Gas system integration is a critical component in the safe, efficient, and reliable transportation and use of natural gas across many industries. It involves connecting various systems, from compressors to pipelines to storage tanks, ensuring that each part works in sync. In today’s world, effective integration is more important than ever as companies seek to balance cost-efficiency with environmental responsibility.
From natural gas transmission systems to renewable energy integration, gas system integration helps reduce energy waste, improve safety, and provide a reliable energy source for both consumers and businesses. With emerging technologies like IoT, AI, and renewable energy sources like biogas and hydrogen, the future of gas system integration is full of promise. It’s all about adapting to change while maintaining stability—and making sure the gas keeps flowing without a hitch.