If you’ve ever wondered how gas pipelines manage to push gases across long distances, or how industrial facilities keep the pressure of gases just right for their operations, then you’re in the right place. Gas booster compressors play a huge role in all of this, and while the tech behind them may seem complicated, understanding how they work doesn’t have to be. Let’s break it down.
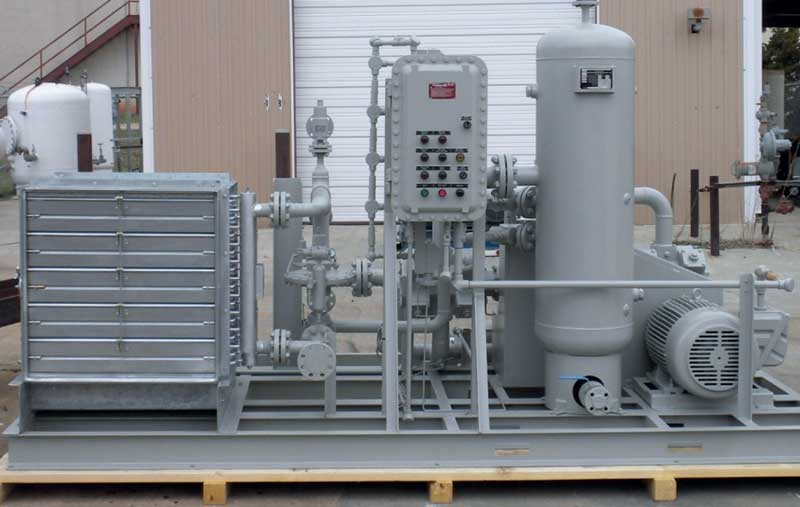
What is a Gas Booster Compressor?
In simple terms, a gas booster compressor is a machine designed to increase the pressure of a gas in a pipeline or storage system. Think of it like a pump for gases, except instead of moving water, it moves gases like air, natural gas, or any other compressed gas. They are used in many industries, from oil and gas to manufacturing and even in some residential applications.
These compressors essentially take the gas at a lower pressure and “boost” it to a much higher pressure so that it can travel long distances or be stored more efficiently. Without them, long-distance gas transportation would be a huge challenge, and we wouldn’t have things like natural gas delivered to our homes.
How Do Gas Booster Compressors Work?
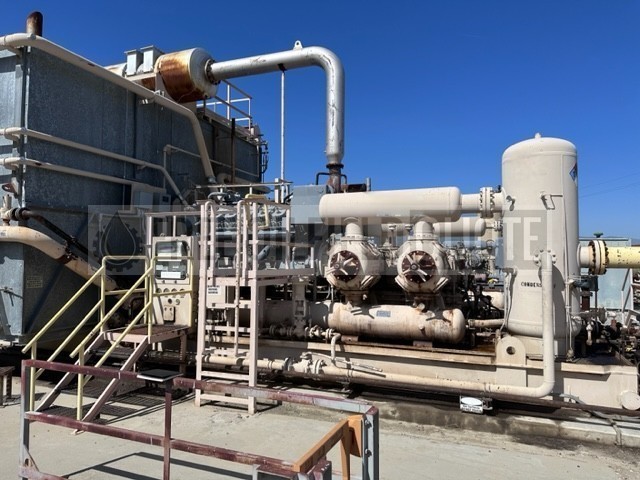
Imagine you’ve got a bunch of gas molecules all moving in a certain direction through a pipe. The faster they move, the more pressure they exert. Gas booster compressors take advantage of this basic principle of physics.
Here’s a simplified version of how they work:
- Compression: The gas enters the compressor chamber, where it’s compressed. This makes the gas molecules get pushed closer together, which increases the pressure.
- Boosting Pressure: The compression process causes the temperature of the gas to rise. This is why gas booster compressors are designed to handle high temperatures. After the gas is compressed, it moves into a smaller, more confined space, which further boosts the pressure.
- Discharge: Finally, the high-pressure gas exits the compressor and moves on to its destination – whether that’s a pipeline, storage tank, or another part of a system.
Types of Gas Booster Compressors
Just like any other type of machinery, there are different kinds of gas booster compressors out there. These compressors come in all shapes and sizes, each suited to specific needs. Let’s take a look at the most common types:
1. Reciprocating Gas Booster Compressors
These are the most commonly used type in industries. They use a piston mechanism to compress the gas. The piston moves back and forth inside a cylinder, pushing the gas into a smaller space, thus increasing its pressure. Reciprocating compressors are often preferred for applications that require high pressure or have varying amounts of gas to compress.
Pros:
- High-pressure capabilities
- Can handle different types of gases
- Relatively efficient for smaller to medium-sized systems
Cons:
- More moving parts (which can mean more maintenance)
- Higher wear and tear compared to other types
2. Centrifugal Gas Booster Compressors
These compressors use a spinning impeller to increase the velocity of the gas, which then gets converted into pressure. Think of them as really fast fans that push the gas through the system. They’re often used in larger-scale industrial applications where there’s a need for continuous gas flow at moderate pressures.
Pros:
- Excellent for handling large volumes of gas
- Less maintenance since there are fewer moving parts
- High efficiency in large systems
Cons:
- Not as effective for high-pressure applications as reciprocating compressors
- Larger footprint and more expensive for small-scale applications
3. Diaphragm Gas Booster Compressors
These are similar to reciprocating compressors but instead of pistons, they use a diaphragm that moves back and forth to compress the gas. These types of compressors are typically used for low-flow, high-pressure applications and are often seen in laboratories, medical facilities, or places that need very clean gas.
Pros:
- No oil or contaminants in the gas stream
- Clean, leak-free design
Cons:
- Limited capacity and flow rate
- Typically more expensive for the performance they offer
Where Are Gas Booster Compressors Used?
Gas booster compressors aren’t just for one type of industry or use case. They are used in a wide range of applications where gas pressure needs to be increased. Let’s go over some of the key places you’ll find them in action:
1. Oil & Gas Industry
In the oil and gas industry, gas booster compressors are a vital part of the process. They help in gas transportation, ensuring that natural gas or other gases are moved across pipelines at a consistent pressure. This can involve both upstream (production) and downstream (refining and distribution) applications.
- Natural Gas Pipelines: These compressors are used to maintain the pressure that keeps the gas moving over long distances.
- Offshore Platforms: Gas compressors are essential for maintaining proper gas flow in offshore oil rigs.
2. Manufacturing & Industrial Plants
In manufacturing plants, gas boosters are used to compress gases for a variety of processes. For instance, they might be used to pressurize air for pneumatic tools or other factory equipment.
- Pressurized Air Systems: Many factories rely on compressed air systems, and gas boosters ensure that the air pressure stays consistent across large areas of the plant.
- Hydrogen Boosting: Some industries require high-pressure hydrogen for processes like hydrogen fuel production.
3. Medical and Laboratory Applications
Gas booster compressors are used in labs and medical environments where gases need to be delivered under precise pressure. For example, medical oxygen is stored at a lower pressure but needs to be boosted before it’s delivered to hospitals or other medical facilities.
4. Food & Beverage
In the food and beverage industry, gases like nitrogen, carbon dioxide, and oxygen are often used in food packaging, beverage carbonation, and preservation. Boosting these gases to the correct pressure is essential for maintaining product quality and shelf life.
5. Renewable Energy
With the rise of hydrogen fuel cells, gas booster compressors are becoming an important part of the renewable energy space. They help compress hydrogen for storage and transportation, enabling cleaner energy production.
Benefits of Gas Booster Compressors
If you’re still wondering why all this gas boosting matters, here are some of the key benefits that these compressors provide:
- Efficient Gas Transport: Boosting gas pressure helps it travel faster and further, reducing the need for multiple compressors along the pipeline.
- Increased Storage Capacity: Compressing gases into smaller spaces allows more gas to be stored in tanks, which is important for everything from energy storage to industrial applications.
- Consistent Pressure: Gas compressors maintain steady pressure levels, which is crucial for ensuring the efficiency of gas-powered systems, machinery, and equipment.
- Safety: Boosting gas pressure to optimal levels prevents leaks and helps ensure that gas systems work safely without causing accidents.
Common Maintenance Issues with Gas Booster Compressors
While gas booster compressors are pretty sturdy, like any machinery, they need regular maintenance to keep running smoothly. Here are some of the most common issues people run into:
- Overheating: If the compressor gets too hot, it can break down or damage other components. This is especially common in reciprocating compressors.
- Vibration and Noise: These can indicate a problem with the compressor’s alignment or internal parts. Regular checks can help prevent this.
- Leaks: Whether it’s from the seals, valves, or piping, leaks can be a real problem, especially if the compressor is handling high-pressure gases.
- Oil Contamination: For compressors that require oil, make sure that the oil doesn’t contaminate the gas. Regular oil changes and checks can prevent this issue.
Gas Booster Compressors: Troubleshooting & Tips for Longevity
While gas booster compressors are built to be tough and reliable, keeping them in tip-top shape is crucial for avoiding unexpected downtime and costly repairs. Regular maintenance and understanding some of the most common problems can go a long way in ensuring that your compressor runs efficiently for years to come. Let’s dive into some simple troubleshooting tips and best practices to help prolong the life of your gas booster compressor.
Common Issues and How to Spot Them
- Inconsistent Pressure Output If your gas booster compressor is having trouble maintaining consistent pressure, it could be a sign of several issues:
- Clogged Filters: A dirty or clogged filter can reduce airflow and cause pressure fluctuations. Regularly check and replace the filters as needed.
- Faulty Pressure Regulator: A malfunctioning pressure regulator can lead to erratic pressure output. It’s essential to test and replace the regulator if you notice any inconsistencies.
- Leaky Valves or Seals: Leaks at any point in the compressor system can cause pressure loss. Listen for unusual hissing sounds, or use soapy water to check for leaks along the piping and seals.
- Excessive Vibration or Noise Vibration and noise are often signs that something is out of alignment, or parts may be worn down:
- Misaligned Components: Over time, parts such as pistons or valves can become misaligned. Check the alignment of your compressor’s moving parts and correct them if needed.
- Worn-out Bearings: Bearings that support the moving parts of the compressor can wear down and cause additional noise and vibration. Periodically check the bearings and replace them when they show signs of wear.
- Loose Mounting: Ensure that the compressor is securely mounted. Loose mounting can amplify vibrations and lead to faster wear on the compressor.
- Overheating Overheating is one of the most common issues in gas booster compressors, especially in reciprocating compressors. When the compressor runs too hot, it can cause internal damage and reduce its lifespan:
- Check Cooling System: Make sure the compressor’s cooling system is working properly. If it uses air cooling, ensure there’s no obstruction around the intake and exhaust vents. For liquid-cooled systems, check the coolant levels and replace fluids as necessary.
- Overuse or Overload: Don’t push your compressor beyond its capacity. Make sure you’re not overloading it with more pressure or flow than it’s rated to handle.
- Dirty Radiators: Dust and debris can clog the radiator, causing the compressor to overheat. Regularly clean the radiator to maintain optimal cooling performance.
- Oil Leaks and Contamination Oil contamination is another issue that can affect gas booster compressors, especially in models that rely on oil for lubrication:
- Inspect Seals and Gaskets: Over time, seals and gaskets can wear down, allowing oil to leak out. Check these parts regularly and replace them when necessary.
- Change Oil Regularly: Regular oil changes are essential to prevent contamination. Follow the manufacturer’s guidelines on oil change intervals, and use the recommended oil type for your compressor.
- Monitor Oil Levels: Keep an eye on oil levels to ensure the compressor has enough lubrication. Low oil levels can cause friction and damage to internal components.
- Pressure Loss in High-Pressure Systems High-pressure systems are particularly sensitive to leaks, and even a tiny gap can cause significant pressure loss:
- Check for Leaks: Leaks in high-pressure systems are a big concern. Use a leak detection solution or pressure gauges to monitor for any loss of pressure in the system.
- Inspect Piping and Fittings: Over time, pipes, fittings, and joints can degrade. Tighten any loose connections and replace corroded or damaged parts.
Best Practices for Maintaining Your Gas Booster Compressor
Now that we’ve covered some common issues, let’s go over a few best practices to keep your gas booster compressor in optimal working condition.
- Follow Manufacturer’s Maintenance Schedule Each compressor model has its own maintenance schedule based on its make and usage. Always follow the manufacturer’s recommended service intervals for tasks like oil changes, filter replacements, and parts inspections. Sticking to the schedule can prevent a lot of common issues from cropping up.
- Regular Inspections Even if your compressor seems to be running fine, don’t neglect routine checks. Inspect things like:
- Air filters
- Oil levels and quality
- Gaskets, seals, and O-rings
- Piping for corrosion, cracks, or leaks
- Keep It Clean Dust, dirt, and grime can wreak havoc on your compressor over time. Make it a habit to regularly clean the compressor’s exterior and surrounding area. Also, make sure the intake and exhaust vents are clear to allow proper airflow for cooling.
- Keep the Compressor Lubricated For compressors that use oil, keeping them properly lubricated is essential for preventing wear and tear. Not only does oil help with moving parts, but it also helps with heat dissipation. Use high-quality oil and avoid overfilling, as too much oil can cause foaming and reduced efficiency.
- Upgrade to Modern Models When Needed Gas booster compressors, like any other technology, can become outdated. If your compressor is old and requiring frequent repairs, consider upgrading to a newer model. Modern compressors are often more energy-efficient, quieter, and have improved safety features that can save you both time and money in the long run.
Gas Booster Compressors in the Future
As industries look to become more energy-efficient and reduce their carbon footprints, gas booster compressors will continue to evolve. Manufacturers are already working on designs that are more energy-efficient, eco-friendly, and require less maintenance. Here are a few trends that are shaping the future of gas booster compressors:
- Energy Efficiency: Expect to see compressors that consume less energy while maintaining the same performance levels. These innovations will help industries reduce costs and contribute to greener practices.
- Smarter Systems: With the rise of Industry 4.0 and the Internet of Things (IoT), gas booster compressors are becoming “smarter.” We’re already seeing systems that can monitor performance, detect issues in real-time, and even predict when maintenance is needed.
- Environmentally Friendly Options: As environmental concerns grow, there will be more emphasis on reducing emissions and minimizing the ecological impact of compressors. New refrigerants and low-energy technologies will continue to improve compressor sustainability.
- Automation: Some systems are becoming fully automated, requiring less human intervention while improving the precision and reliability of gas boosting. This is particularly useful in large-scale industrial operations where consistent performance is key.
Final Thoughts: Why Gas Booster Compressors Matter
Gas booster compressors are truly unsung heroes in many industries. From ensuring that natural gas is delivered efficiently to your home, to helping manufacturers power their machines, they’re an essential part of modern industrial life. And while they may not be the flashiest part of the system, their reliability and performance are crucial to keeping everything running smoothly.
Understanding the basics of how these compressors work, how to maintain them, and their role in various industries will help you make smarter decisions when it comes to using or investing in this equipment. Whether you’re operating a factory, maintaining a pipeline, or working with clean energy, gas booster compressors will continue to play a vital role in the future of energy and industry.
By taking care of your compressor and staying ahead of potential issues, you’ll ensure that it provides reliable, efficient performance for years to come. So, the next time you hear that hum of a compressor in the background, you’ll know exactly why it’s there – boosting pressure and helping keep everything in motion!
Conclusion
Gas booster compressors might seem complicated at first glance, but they play a crucial role in many industries by providing a reliable way to increase gas pressure. From maintaining gas flow through pipelines to ensuring your manufacturing processes run smoothly, they are indispensable tools for today’s industrial world.
By understanding the basics of how gas booster compressors work, their different types, and where they are used, you can appreciate how they contribute to everything from the gas you use in your home to the clean energy systems of the future. So, next time you see a gas pipeline or industrial facility, you can bet there’s a booster compressor somewhere nearby, doing its part to keep things running smoothly!