Liquefied natural gas (LNG) has become one of the most important energy sources in recent years, especially as global demand for cleaner, more sustainable alternatives to coal and oil has increased. LNG is natural gas that’s been cooled down to liquid form, making it easier to store and transport. But before natural gas can be turned into LNG, it goes through a complex processing journey. If you’ve ever wondered how natural gas becomes the LNG that powers homes, industries, and even vehicles around the world, this article will walk you through the process in a simple, digestible way.
What is LNG?
To start, let’s briefly cover what LNG is. Natural gas is primarily made up of methane (CH4), along with small amounts of other hydrocarbons like ethane, propane, and butane. Natural gas is typically found deep underground or in shale rock formations. It’s often extracted and used in its gaseous state, which can be problematic for storage and transportation, especially if you need to move it across vast distances, such as from offshore oil rigs to far-away markets.
This is where liquefaction comes in. By cooling natural gas to around -162°C (-260°F), it turns into a liquid, reducing its volume by about 600 times. This makes LNG much easier and safer to transport in bulk, especially over long distances via ships, trucks, or rail. Once it reaches its destination, it’s regasified and used for energy, heating, cooking, and even as a cleaner fuel alternative for vehicles.
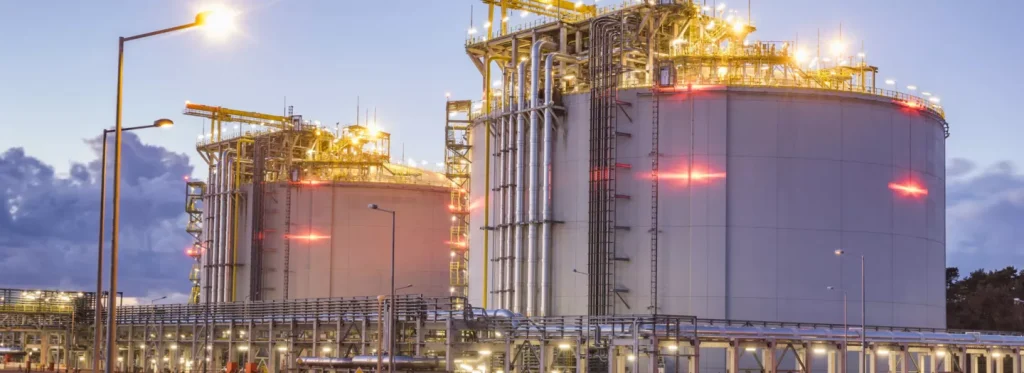
Now, let’s take a closer look at the journey LNG goes through to get from raw natural gas to the liquid form that’s transported around the world.
Step 1: Gathering and Cleaning Natural Gas
Before natural gas can be liquefied, it needs to be gathered and cleaned. The raw natural gas that comes out of the ground is far from pure. It typically contains impurities like water, carbon dioxide, hydrogen sulfide, and other trace elements. These impurities need to be removed to ensure the gas can be safely processed, stored, and transported.
The first step is gathering the gas. This is usually done at the wellhead, where the natural gas is collected through pipelines. It may also come from offshore rigs or storage facilities where natural gas is stored under pressure.
Once the gas is gathered, the first phase of processing begins. The goal here is to remove contaminants and other materials that might hinder the liquefaction process or damage equipment down the line. Here’s how the cleaning process works:
- Separation of Liquids and Solids: Raw natural gas can contain liquids and solids, like water and oil. These need to be separated out before further processing. This step is typically done with separators, where the gas is filtered to remove these elements.
- Removal of Acid Gases: Acid gases like hydrogen sulfide (H2S) and carbon dioxide (CO2) are corrosive and must be removed to ensure that the gas is safe to handle. Special equipment like amine scrubbers or solvent absorption processes is used to “scrub” the gas and remove these impurities.
- Dehydration: Water in the natural gas can form ice crystals at low temperatures during liquefaction, which could block pipes or cause equipment to malfunction. So, water is typically removed using a dehydration process, where the gas is passed through materials that absorb moisture, leaving the gas dry and ready for the next stage.
Step 2: Liquefaction
Once the natural gas is cleaned, it’s ready for liquefaction. Liquefaction is the heart of the LNG process, and it’s where natural gas is cooled down to become liquid. The cooling process might sound simple, but it requires a lot of energy and specialized equipment. Here’s how it works:
- Cooling to -162°C: To convert natural gas into LNG, the temperature must be dropped to around -162°C. At this temperature, methane becomes a liquid, and the gas shrinks to about 1/600th of its original volume. This is done through a series of refrigeration cycles using various cooling methods.
- Pre-cooling: Before the natural gas reaches -162°C, it’s pre-cooled using a staged cooling process. First, the gas is cooled to temperatures around -30°C to -50°C. At this stage, much of the larger impurities, like heavier hydrocarbons, condense and can be separated from the gas.
- Compression and Expansion: In the next stage, compressors are used to cool the gas further by compressing it. The compressed gas is then passed through a series of heat exchangers, where it’s gradually cooled down until it reaches the desired temperature for liquefaction.
- Liquefaction Cycles: There are different technologies used for liquefaction, like the Cascade Process, Mixed Refrigerant Process, and Propane Pre-cooled Mixed Refrigerant Process. These methods use different types of refrigerants, often combining propane, nitrogen, and methane, to progressively cool the gas to the liquid state.
The entire liquefaction process requires a massive amount of energy, but it’s what makes LNG possible and practical for long-distance shipping.
Step 3: Storage and Transportation
After liquefaction, the LNG is stored in specialized tanks before being transported to its destination. Because LNG is so cold, it requires tanks made from materials that can withstand extremely low temperatures. These storage tanks are usually double-walled and insulated, with the inner tank being made from a material like steel or aluminum.
LNG is typically transported in two main ways:
- By Ship: Large LNG carriers, or LNG tankers, are used to ship the liquid gas across oceans. These ships are specially designed with insulated tanks to keep the LNG at its low temperature during the journey. LNG tankers have a variety of sizes, but the largest ones can hold up to 266,000 cubic meters of LNG.
- By Truck or Rail: For shorter distances, LNG can be transported by trucks or rail in cryogenic tanks. This is typically used when LNG needs to be delivered to remote locations or smaller markets.
While the LNG itself is in a liquid state, it still needs to be kept at a low temperature throughout transportation to prevent it from turning back into a gas.
Step 4: Regasification
Once LNG reaches its destination, it has to be regasified before it can be used for energy production or distribution. Regasification is the process of converting LNG back into its gaseous form so that it can be transported via pipelines to homes, businesses, and industries.
The regasification process generally involves the following steps:
- Warming the LNG: LNG is warmed up by passing it through heat exchangers. These exchangers use seawater or other sources of heat to gradually increase the temperature of the LNG until it turns back into gas.
- Compression and Distribution: Once the LNG has been regasified, it’s compressed and then moved through pipelines for distribution. The gas can now be used for cooking, heating, or power generation just like regular natural gas.
- Quality Control: During regasification, the gas is also monitored for quality to ensure it meets the standards for safe and efficient use. Any remaining impurities or contaminants that may have been introduced during transport are removed during this stage.
Step 5: Environmental and Safety Considerations
Although LNG is often seen as a cleaner alternative to other fossil fuels, it’s important to consider the environmental and safety factors involved in its processing, storage, and transportation.
- Environmental Impact: While LNG itself burns cleaner than coal or oil, the processes involved in its production, liquefaction, transportation, and regasification all require energy. These processes can lead to greenhouse gas emissions, especially if fossil fuels are used to power the equipment. However, LNG is still considered a much cleaner alternative to coal and oil, producing fewer emissions and pollutants.
- Safety: Because LNG is so cold and stored under pressure, it’s crucial to handle it with care. Safety measures are strictly enforced during every stage of the process, from the initial extraction to the final regasification. In the event of a spill or leak, LNG can cause severe burns, and the area around the leak must be evacuated immediately.
LNG plants are designed with various safety protocols, including advanced leak detection systems, fire suppression systems, and emergency shutdown procedures. Regular safety drills and maintenance are essential to ensure everything runs smoothly.
Conclusion
The journey from natural gas to LNG involves several steps, each of which requires specialized equipment and expertise. From cleaning the raw natural gas to cooling it to -162°C for liquefaction, storing and transporting it safely, and finally regasifying it for use—there’s a lot that goes into making LNG a reliable energy source.
LNG has revolutionized the way natural gas is transported and used across the world. It’s safer, more efficient, and better for the environment than many other fossil fuels. While the technology behind LNG processing is complex, it’s an essential part of the global energy landscape.
As demand for cleaner energy sources continues to rise, LNG will likely play a central role in the transition toward a more sustainable future. Whether it’s being used to heat homes, power industries, or fuel vehicles, LNG offers a cleaner, more efficient option for meeting the world’s energy needs.