Anyone who’s worked in the gas compression industry knows that compressors are no small players when it comes to energy use. These machines—whether they’re moving gas through pipelines or pressurizing air for industrial processes—consume a lot of power. But here’s the kicker: they also produce a ton of heat during operation. Now, while that heat might seem like a byproduct to be ignored or dealt with, what if we told you it could actually be used as a resource? Yep, that’s right—heat recovery from gas compression processes is not only possible, but it’s also a game-changer for businesses looking to reduce energy consumption and boost efficiency.
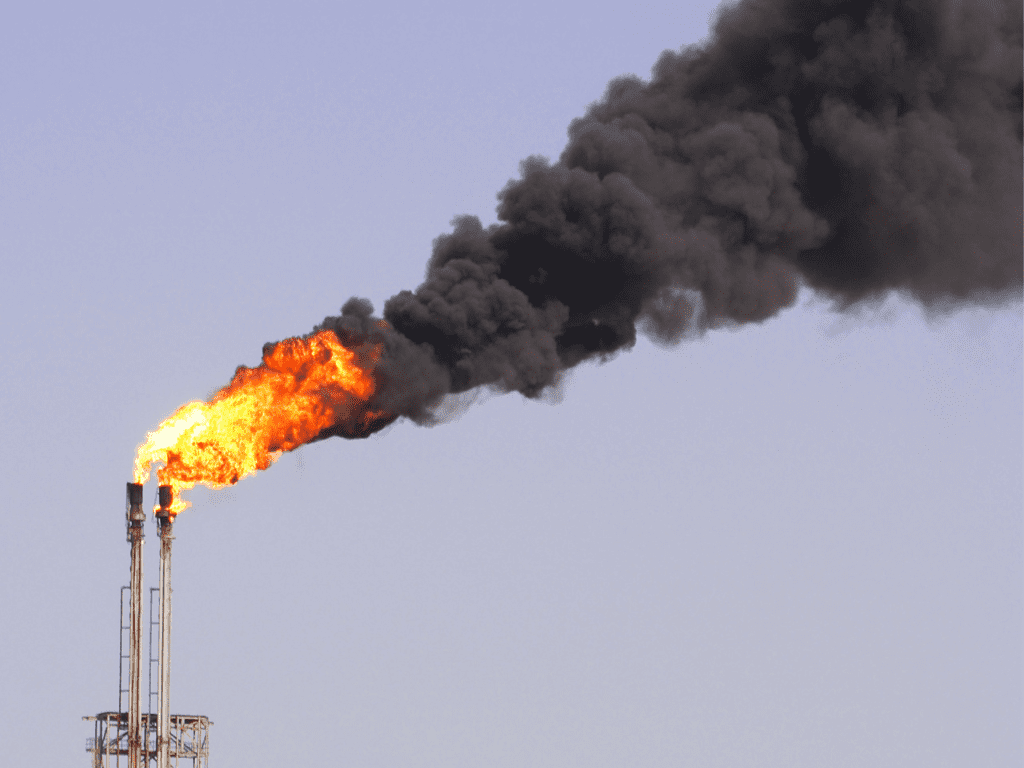
In this article, we’re going to break down what heat recovery from compressors is all about, why it matters, and how you can take advantage of this often-overlooked source of energy to save money and improve your operations.
What is Heat Recovery in Gas Compression?
To understand the concept of heat recovery, we need to first talk about how compressors work. Gas compressors are designed to increase the pressure of gas by reducing its volume, and this process generates a lot of heat. Whether you’re using a reciprocating compressor, screw compressor, or centrifugal compressor, all of them produce excess heat as they work.
Now, this heat isn’t just something you can wish away. It’s energy, and it’s often wasted if not captured and used effectively. Heat recovery involves collecting this waste heat from the compressor and redirecting it to another part of the system, where it can be used for various purposes like:
- Preheating fluids (such as oil, water, or even natural gas)
- Generating electricity via a heat-to-power system
- Heating the building or nearby spaces
- Boosting other industrial processes that require heat (like drying or distillation)
The idea is simple: instead of letting the heat escape into the air or using a traditional cooling system to get rid of it, you capture and repurpose it, making the system more energy-efficient overall.
Why Is Heat Recovery Important?
You might be wondering, “Okay, but why bother with heat recovery in the first place?” Let’s break down a few reasons why it’s such a big deal.
1. Energy Efficiency
Gas compression is an energy-intensive process. Compressors need to be powered 24/7 in many industries, which can significantly increase operating costs. However, the heat they produce is essentially wasted energy—energy that could be used elsewhere in the process. By capturing this heat, you can reduce the need for additional fuel or electricity to power other systems. This makes your operation more energy-efficient, lowering costs and helping your business stay competitive.
2. Cost Savings
Using recovered heat for other processes or heating needs means you don’t need to spend extra money on energy sources for those activities. For example, if you can use the waste heat to preheat air or fluids, you reduce the amount of electricity, gas, or steam needed to bring those materials up to temperature. Over time, this leads to significant cost savings—which, in any industry, is always a win.
3. Environmental Impact
Energy consumption in industries like gas compression contributes to a larger carbon footprint. By implementing heat recovery systems, you’re essentially reducing the amount of energy you need from external sources. This lowers your overall energy demand and carbon emissions, which is great for the environment. Plus, some countries even offer tax incentives for companies that take steps to reduce their environmental impact, so it could benefit your bottom line in more ways than one.
4. Long-Term Sustainability
By reducing waste and improving energy efficiency, heat recovery systems help ensure that your operations are more sustainable in the long run. Companies that rely on outdated or inefficient processes are not only paying more for energy, but they’re also more likely to experience system breakdowns and increased downtime. Heat recovery can extend the life of your equipment by preventing overheating and reducing wear on the system. This leads to reduced maintenance costs and a longer equipment lifespan.
How Does Heat Recovery Work?
Now that we know why heat recovery is important, let’s talk about how it actually works. In gas compression processes, the heat recovery system usually involves a few key components:
1. Heat Exchangers
The most common tool used in heat recovery systems is a heat exchanger. These devices are designed to transfer heat from one medium (like hot gas or coolant) to another (such as water, air, or oil). In the case of gas compressors, a heat exchanger can capture heat from the compressed gas or exhaust gases and transfer it to a different medium that needs heating.
For example, in many industrial setups, a heat exchanger may capture the heat from the compressor’s exhaust gases and transfer that heat to water. The heated water can then be used for other processes or even to warm the building.
2. Thermal Oil Systems
In some advanced systems, thermal oil is used as a heat transfer medium. Thermal oil can carry heat over long distances without losing temperature, making it useful for larger operations. The oil is heated by the compressor’s exhaust, and it can then be circulated through a system to preheat other equipment or to provide heat for nearby areas.
3. Combined Heat and Power (CHP) Systems
Some businesses take heat recovery to the next level by implementing Combined Heat and Power (CHP) systems, also known as cogeneration systems. These systems use the heat from the compressor not just for preheating but to generate electricity. Essentially, CHP systems capture waste heat and convert it into electrical power through steam turbines or organic Rankine cycle (ORC) systems. This can offset your energy use, lowering your utility bills.
4. Regenerative Systems
Regenerative heat exchangers are designed to capture and store heat during the compression cycle. The stored heat is then released at the right moment to support other processes. These systems often use ceramic or metal materials to store heat and are especially efficient when paired with compressors that operate continuously or at variable speeds.
Common Applications of Heat Recovery in Gas Compression
Heat recovery in gas compression processes isn’t a one-size-fits-all solution. Different industries use the recovered heat in various ways, depending on their specific needs. Here are some common applications:
1. Natural Gas Processing
In natural gas processing, compressors are used to move gas through pipelines and refine it. The heat generated by these compressors can be used to preheat incoming gas before it enters processing units, reducing the need for additional fuel to heat the gas. This is especially valuable when the gas needs to be cooled or compressed again later in the process.
2. Power Generation
Many power plants use large-scale gas compressors as part of their operations. Here, heat recovery can be used to preheat combustion air or boost boiler efficiency, reducing the overall fuel requirements. In some cases, the recovered heat can be used to generate additional electricity through steam turbines in a CHP system.
3. Industrial Manufacturing
Manufacturers that rely on compressed air or gas systems often use heat recovery to preheat air before it enters other machinery, reducing energy consumption. For example, in industries like food processing, where large amounts of steam and heat are required, waste heat from compressors can be used to provide that energy. In chemical manufacturing, heat recovery can be used to boost reaction rates or to provide the necessary heat for distillation processes.
4. Building Heating and Hot Water
Some companies with large-scale compressor systems use recovered heat to provide hot water or space heating for their buildings. This is particularly beneficial in colder climates, where heating costs can be high. Capturing heat from compressors not only reduces utility bills but also creates a more comfortable work environment for employees.
Benefits of Heat Recovery
At this point, it’s clear that heat recovery is an excellent option for many businesses. Let’s recap some of the main benefits:
- Lower Energy Costs: By recovering heat, you reduce the amount of energy needed from external sources, leading to lower electricity or gas bills.
- Improved Efficiency: Heat recovery makes your compressor system more efficient by reducing waste and repurposing energy that would otherwise be lost.
- Environmental Benefits: By using less energy and emitting fewer carbon gases, heat recovery is an eco-friendly solution.
- Extended Equipment Lifespan: Keeping temperatures in check with heat recovery reduces wear and tear on the compressor system, leading to fewer breakdowns and lower maintenance costs.
- Increased Sustainability: By optimizing energy use, businesses that implement heat recovery are more sustainable in the long term, improving their reputation and helping them meet regulatory standards.
Challenges of Heat Recovery
While heat recovery has many advantages, it’s not without its challenges. Some of the most common issues businesses face when implementing heat recovery systems include:
- Initial Costs: Setting up a heat recovery system, especially for larger operations, can require a significant upfront investment.
- Maintenance: Heat recovery systems require regular maintenance to ensure they are functioning properly. Heat exchangers, for example, can accumulate sludge and debris that need to be cleaned regularly.
- Complexity: Integrating heat recovery systems with existing equipment can be complex and might require adjustments to your workflow or processes.
Real-World Examples of Heat Recovery in Gas Compression
While the theory behind heat recovery is compelling, it’s always good to see how these systems work in the real world. Here are some examples from industries that have successfully integrated heat recovery into their gas compression processes, proving that the investment is well worth it.
1. Natural Gas Industry:
In the natural gas industry, gas compressors play a crucial role in moving natural gas through pipelines and preparing it for various uses, including energy generation and heating. Heat recovery is a natural fit here, as large compressors are in constant use, producing significant amounts of waste heat.
One example comes from a natural gas processing plant in the U.S., where compressors are used to compress raw gas before it enters processing units. The heat generated by these compressors was initially vented into the atmosphere, leading to wasted energy. However, the facility decided to implement a heat recovery system that repurposed the waste heat for preheating incoming gas. This reduced the amount of energy required for subsequent processing steps, cutting down on the plant’s fuel costs by 15-20%.
Additionally, the recovered heat was used to heat water for onsite facilities, reducing the plant’s reliance on external energy sources. This change not only saved the company money but also lowered their carbon emissions, aligning with environmental goals and making them more competitive in the market.
2. Manufacturing:
In industrial manufacturing settings, heat recovery from gas compressors can be used to preheat air for other equipment or to provide process heat for various production activities. For instance, a metal fabrication facility that relied on compressed air to power machinery found itself facing rising energy costs due to the inefficiency of its equipment.
After implementing a heat recovery system, the company began recovering heat from its air compressors and used it to preheat incoming air before it entered their pneumatic systems. This simple change resulted in a 15% reduction in overall energy consumption. They also recovered heat for use in space heating, allowing them to reduce the use of their gas-fired heating systems. The facility reported a significant decrease in both operational costs and energy waste, which helped improve the company’s profit margins.
3. Chemical Manufacturing:
Chemical production facilities often involve highly energy-intensive processes that require both heat and power. A chemical plant that utilized gas compressors to pressurize chemical reactors began capturing the waste heat from these compressors to fuel the plant’s boiler system. The heat recovery system diverted the excess heat to generate steam, which was then used for distillation and other heat-based processes.
This system not only lowered the plant’s reliance on external energy sources but also allowed the plant to generate more steam without consuming additional fuel, which is a win in terms of both efficiency and sustainability. As a result, the chemical plant was able to cut its fuel consumption by around 10% annually while improving the overall safety of the system by reducing the need for high-temperature operations.
How to Implement a Heat Recovery System
Implementing a heat recovery system might sound complicated, but with the right planning and technology, it can be a straightforward process. Here’s a step-by-step guide to get you started:
1. Assess Your Current System
Before making any changes, you need to assess your current setup. Take a detailed look at your gas compressors and other energy-intensive equipment. Identify where heat is being produced and where it could potentially be captured.
- How much heat is being generated? Measure the temperature and flow of exhaust gases and fluids to determine how much heat you can recover.
- What’s your current energy usage? Review your utility bills and energy consumption reports to see where improvements can be made.
- What needs heat? Identify parts of your system or facility that would benefit from the recovered heat, such as preheating materials, water, or even space heating for the building.
2. Choose the Right Heat Recovery Technology
Once you’ve identified areas for improvement, it’s time to choose the right technology for heat recovery. Here are a few options to consider:
- Heat Exchangers: A common choice, heat exchangers are great for transferring heat from one medium to another. If your compressors are producing heat that could be transferred to fluids (such as water or thermal oil), this is an efficient solution.
- Combined Heat and Power (CHP) Systems: If you want to take things a step further and generate electricity from your recovered heat, a CHP system can convert waste heat into usable power. This is a more complex solution but could be highly beneficial for larger facilities.
- Regenerative Systems: These systems store heat during the compression cycle and release it when needed. They’re typically used in systems where heat demand is constant or predictable.
- Thermal Oil Systems: For industries with high thermal demands or long-distance heat transport needs, thermal oil systems can transfer heat over long distances with minimal heat loss.
3. Design the Integration
Now comes the integration phase. Whether you’re adding a heat exchanger or installing a CHP system, you need to ensure that the new technology is properly integrated into your existing setup. This may require modifications to your piping, ducting, or even electrical systems.
- Consult with experts: It’s highly recommended to work with engineers or specialists who can help design and implement the system correctly. This ensures that the heat recovery system is properly sized and integrated for optimal performance.
- Ensure safety: Adding new components to your system should not compromise safety. Make sure that the heat recovery system is designed to handle high temperatures and pressures without increasing the risk of overheating or failure.
4. Monitor and Optimize Performance
Once your heat recovery system is installed, it’s important to monitor its performance. This includes tracking the amount of heat recovered, energy savings, and any changes in system efficiency. Regular monitoring ensures that the system is operating as expected and allows you to identify areas for optimization.
- Use sensors: Install temperature and flow sensors to monitor heat recovery performance in real-time.
- Track energy savings: Compare your energy consumption before and after installation to evaluate the financial impact of the system.
- Maintain the system: Heat exchangers and other components require regular maintenance to ensure they’re working efficiently. Cleaning, lubricating, and checking for leaks are crucial tasks to keep the system running smoothly.
Overcoming Common Challenges
While the benefits of heat recovery are clear, there are some challenges that companies may face when implementing these systems:
1. Initial Costs and ROI
The upfront investment for installing heat recovery systems can be high. The cost of purchasing and installing equipment like heat exchangers, thermal oil systems, or CHP systems can add up. However, the long-term return on investment (ROI) from reduced energy bills, lower operational costs, and extended equipment life often justifies the expense.
2. Space Constraints
Heat recovery systems require space for equipment like heat exchangers or thermal oil tanks. In some facilities, finding room for these systems can be challenging, especially if space is already limited. Planning the layout and ensuring proper integration with your existing systems will be important to overcome this obstacle.
3. Complexity of Integration
Integrating a heat recovery system into an existing compressor setup can sometimes be complex. It may require reworking parts of the system, adjusting operating procedures, or retraining staff. That said, with proper planning and support from experts, this challenge can be managed effectively.
4. Maintaining System Efficiency
Heat recovery systems need regular maintenance to ensure they continue to operate efficiently. If not properly maintained, they could become less effective over time, leading to reduced heat recovery and energy savings. Scheduling regular checks and preventive maintenance will ensure the system continues to perform optimally.
Conclusion: The Future of Heat Recovery
Heat recovery in gas compression processes is rapidly becoming a must-have for industries looking to improve energy efficiency, cut costs, and reduce their environmental footprint. By capturing waste heat from compressors and using it in productive ways, businesses can unlock significant savings, improve operational sustainability, and reduce their reliance on external energy sources.
As technologies evolve, we can expect even more advanced heat recovery systems that are smarter, more efficient, and easier to integrate into existing operations. Whether you’re in natural gas, manufacturing, or power generation, taking advantage of heat recovery can help future-proof your business and give you an edge in a competitive, energy-conscious market.
The key takeaway? Heat recovery is not just about saving a few bucks here and there; it’s about transforming an often-overlooked waste product (heat) into a valuable resource. So, don’t let that heat go to waste—harness it, and turn it into an asset that helps your business run more efficiently and sustainably.
Heat recovery from gas compression processes is more than just a good idea—it’s a smart strategy for businesses looking to reduce costs, improve efficiency, and boost sustainability. Whether you’re in the natural gas industry, manufacturing, or power generation, capturing and repurposing waste heat can save you a ton of energy, money, and environmental impact.
By using tools like heat exchangers, thermal oil systems, and CHP technology, businesses can unlock the full potential of their gas compression systems, turning excess heat into a valuable resource. Yes, it requires an investment upfront, but the long-term benefits—ranging from reduced energy consumption to extended equipment life—are more than worth it.
So, if you’re still letting all that heat go to waste, it might be time to rethink your approach. Heat recovery is a simple, effective, and sustainable way to make your operation smarter and more cost-effective.