When you think of a gas compressor, you probably picture a huge machine humming away in an industrial facility or maybe even a noisy, vibrating unit in a pipeline system. It’s true – gas compressors are notorious for making a lot of noise. But why does this happen, and more importantly, what can we do about it?
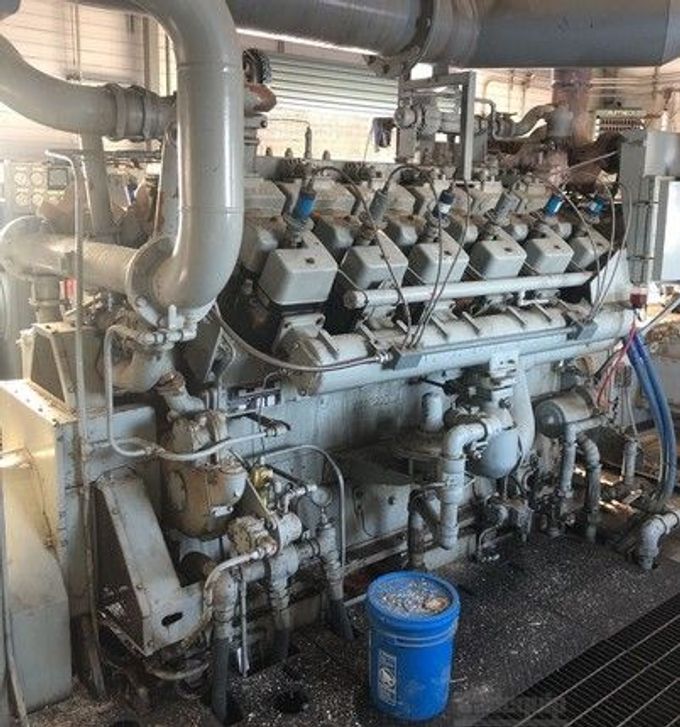
The Big Deal About Compressor Noise
Gas compressors are used in a ton of industries – from oil and gas to manufacturing, and even food production. They help push gas through pipelines, store natural gas, or ensure that various systems get the pressurized air they need to run smoothly. But while they’re doing their job, they can also create a fair amount of noise, which isn’t just an annoying byproduct. It can actually cause a whole lot of problems.
First off, compressor noise can be dangerous. Prolonged exposure to loud sounds can lead to hearing damage for workers who are around these systems daily. Over time, this could result in health and safety issues, and that’s something nobody wants to deal with.
Also, noise pollution from compressors can interfere with nearby operations, disturb the local community, or even result in legal complaints. And don’t forget about the energy efficiency side of things – a noisy compressor might be an inefficient one too, since excessive vibration and sound often mean energy is being wasted.
So, Why Are Compressors So Noisy?
Before diving into the solutions, let’s understand where all this noise is coming from. Noise in gas compressors typically originates from a few key sources:
- Vibration: Compressors have moving parts, and when these parts – like pistons, rotors, or gears – are in action, they cause vibrations. These vibrations travel through the machine and even the floor or walls of the building. The more forceful the vibration, the louder the sound.
- Pressure Changes: Compressors work by creating high pressure to push gas into pipelines or storage. As the gas moves through the system, the sudden changes in pressure – especially when gas enters or exits valves – can create air turbulence, which turns into noise.
- Rotational Motion: In certain types of compressors, like rotary or screw compressors, the rotating motion of the parts is a significant source of noise. These rotating components constantly rub against each other, creating friction, which contributes to the sound.
- Air and Gas Flow: The flow of air or gas through the compressor system itself can generate noise, particularly if the flow is fast and turbulent. The quicker the gas is being compressed, the noisier the machine will tend to be.
How Do We Tackle This Noise?
Now that we know why compressors can get so loud, let’s look at how to reduce that noise. Fortunately, there are a variety of strategies and technologies that can help bring the noise level down.
1. Sound Enclosures and Barriers
One of the simplest and most effective ways to reduce compressor noise is by using soundproof enclosures. These are physical barriers built around the compressor to contain and absorb the sound. Enclosures are designed with materials that block or absorb sound waves, such as acoustic foam or fiberglass insulation.
By trapping the noise within the enclosure, the sound is prevented from escaping into the surrounding environment, making the area much quieter. These enclosures can be custom-built to fit the specific compressor and the space it’s operating in.
2. Anti-Vibration Mounts
Vibration is a big contributor to compressor noise, so dealing with it directly can make a huge difference. One solution is using anti-vibration mounts. These mounts are designed to absorb the vibrations from the compressor and prevent them from being transmitted through the building or structure.
You can also use vibration-damping materials like rubber or elastomers underneath the compressor unit. This helps reduce the amount of noise that gets transferred to the surrounding environment.
3. Quiet Compressor Models
Not all compressors are built the same, and some models are actually designed to be quieter than others. If you’re starting from scratch or upgrading equipment, it’s worth looking into quieter options. Oil-free compressors and centrifugal compressors are often quieter than traditional piston compressors because they use different mechanisms for gas compression.
For example, piston compressors, with their constant reciprocating motion, are typically noisier than rotary screw compressors, which use smooth, continuous motion to compress gas. While quieter models may come with a higher price tag, the reduction in noise might make the investment worthwhile in the long run, especially in noise-sensitive areas.
4. Using Noise Barriers and Acoustic Panels
Sometimes, it’s not enough to just enclose the compressor. You may also need to consider placing noise barriers around the machine. These barriers act as additional walls that absorb or reflect sound waves, preventing them from spreading.
Acoustic panels can be installed on walls, ceilings, or other surfaces nearby to further absorb sound and prevent it from bouncing around the room. The material choice is key here – look for materials with high sound absorption qualities like dense foam or mineral wool.
5. Optimizing Compressor Maintenance
Did you know that a lot of noise comes from compressors that aren’t properly maintained? Worn-out parts like bearings, seals, or valves can increase friction and cause additional vibration, which makes everything louder. Regular maintenance checks and keeping parts lubricated properly can go a long way in reducing unnecessary noise.
For instance, oil lubrication helps reduce friction between moving parts, which reduces wear and tear and noise. Keeping parts clean and replacing worn-out components will keep the machine running smoother and quieter.
6. Control the Airflow
Another factor that plays into compressor noise is how the air or gas flows through the system. If the airflow is turbulent or irregular, it can increase noise levels significantly. Ensuring that pipes are smooth, well-designed, and free from obstructions helps the air flow more evenly, reducing turbulence and noise.
You can also install flow silencers or mufflers in the system. These are devices that help smooth out airflow and absorb noise from the gas as it moves through pipes or valves. They’re particularly useful in large systems where you have multiple compressors working at the same time.
7. Enclose the Entire System
Sometimes, it’s not just the compressor that’s noisy, but the whole system. Consider building an enclosure around the entire gas compression unit, including the pumps, motors, and other components. This way, you’ll be tackling the noise from all sources in one go, reducing the overall sound output of the entire operation.
The Benefits of Noise Reduction
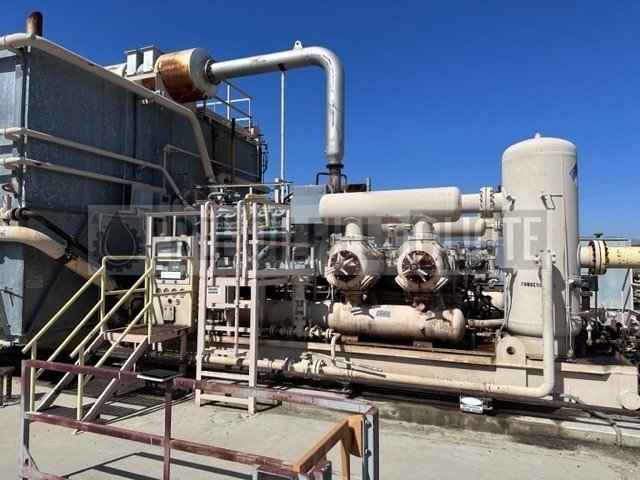
So, why go through all the trouble of reducing compressor noise? Here are a few solid reasons:
- Worker Health and Safety: Reducing noise lowers the risk of hearing loss and improves overall working conditions for employees.
- Compliance with Regulations: Many countries have noise pollution regulations, and reducing noise helps avoid legal problems.
- Increased Productivity: Quieter environments are less stressful and can boost employee productivity and morale.
- Better Relationships with Neighbors: In industrial or commercial areas, cutting down on noise makes it less likely that you’ll annoy nearby businesses or residential areas.
- Improved Equipment Longevity: Many noise-reducing techniques also help improve the longevity of your equipment. For example, vibration reduction can decrease wear and tear on your compressor, keeping it running smoothly for longer.
Advanced Technologies for Noise Reduction in Gas Compressors
While the strategies we’ve discussed so far—like enclosures, anti-vibration mounts, and better compressor models—are effective in most cases, there are also some cutting-edge technologies that can take noise reduction to the next level. Let’s dive into these advanced solutions.
1. Active Noise Control (ANC)
Active Noise Control (ANC), also known as anti-noise technology, is an exciting solution that’s becoming more common in various industrial applications, including gas compressors. The idea behind ANC is simple: you use sound waves to cancel out unwanted noise. This technology is based on the principle of phase inversion, where sound waves are generated that are opposite to the offending noise. When these opposite sound waves meet the noise, they cancel each other out.
For gas compressors, ANC systems can be installed around the compressor or inside the enclosure. Microphones detect the noise level, and a controller generates the inverse sound wave, which is then played through speakers positioned strategically. While ANC is still somewhat niche and expensive, it’s showing promising results in terms of reducing specific frequencies and tackling persistent, low-frequency noise.
2. Variable Speed Drives (VSD)
One of the main causes of compressor noise is the high-speed operation of certain components, particularly in centrifugal and reciprocating compressors. Variable Speed Drives (VSDs) are increasingly being used to control the speed of compressors. VSDs adjust the motor speed to meet demand, instead of running at full capacity all the time.
This not only improves energy efficiency but also reduces noise levels. When the compressor operates at lower speeds, it generates less noise. In fact, many modern compressors come with VSDs to help balance both energy consumption and noise output. For industries that run compressors in 24/7 operations, this can make a noticeable difference in overall sound levels.
3. Noise-Reducing Coatings
Another innovative approach involves the use of noise-reducing coatings on compressor components. These coatings are designed to absorb sound and reduce the impact of vibrations. Some coatings are applied directly to the metal surfaces of compressors or pipes where friction and vibration are most likely to occur.
These coatings are often made from specialized composites that are engineered to reduce noise emissions while also improving durability. Not only do they help reduce the sound produced by the compressor, but they also provide additional protection against wear and tear, which can extend the lifespan of the equipment.
4. Advanced Mufflers and Silencers
While mufflers and silencers have long been used to reduce noise in exhaust systems, newer, more advanced versions are being developed specifically for gas compressors. These devices are designed to absorb sound waves produced by gas flows and venting. Modern mufflers use multi-chamber designs that increase the absorption of high-frequency noise, while also being more effective in dampening lower-frequency sounds, which tend to be the hardest to eliminate.
Moreover, some mufflers are equipped with sound-damping materials like acoustical foam, metal baffles, and resonators that make the entire gas flow process quieter. High-quality mufflers can significantly reduce noise without compromising the compressor’s performance, which is a win-win for any industrial setup.
How Noise Reduction Can Improve Your Bottom Line
Implementing noise reduction measures for gas compressors doesn’t just help with noise pollution—it can have real financial benefits as well. Let’s take a closer look at how investing in quieter, more efficient systems can ultimately save money in the long term.
1. Reduced Energy Costs
Although installing noise-reduction technologies like soundproof enclosures or using VSD compressors might have an upfront cost, they can lead to lower energy bills. For example, compressors that run more efficiently (thanks to VSDs) use less power, which saves on energy consumption.
Additionally, when you reduce vibrations and friction within compressors, the system runs more smoothly, and less energy is lost to unnecessary mechanical movement. In the long run, this improved efficiency can pay off through lower operational costs and longer equipment lifespans.
2. Reduced Maintenance Costs
Noise is often a sign of wear and tear or inefficient operation. A noisy compressor could mean that parts are rubbing together more than they should, causing friction, increased energy use, and potentially damaging components. By reducing noise, you’re also catching signs of system inefficiency early, allowing for timely maintenance and repairs.
Compressor systems that are regularly maintained and monitored for noise reduction will require fewer repairs, leading to less downtime and fewer costs associated with major component replacements. It’s a smart way to protect your investment and ensure you’re getting the most out of your equipment.
3. Enhanced Worker Productivity and Satisfaction
Noise can have a negative impact on employee health, which can eventually affect productivity. When workers are exposed to high levels of noise for long periods, they are more likely to experience stress, fatigue, and even hearing loss, all of which can reduce workplace efficiency and lead to higher turnover rates.
By reducing compressor noise, you create a more comfortable and safer working environment. This, in turn, can lead to higher employee satisfaction, fewer sick days, and improved performance. When workers are more comfortable, they’re more focused and less likely to experience distractions caused by noise, which can lead to increased productivity.
4. Improved Regulatory Compliance
In many regions, noise pollution regulations are becoming stricter, especially in industrial zones or residential areas. Companies that fail to comply with these regulations could face fines or even be forced to shut down operations until noise levels are reduced.
By investing in noise reduction solutions now, companies can avoid potential fines and legal battles later. Furthermore, adhering to environmental noise regulations enhances a company’s reputation and shows a commitment to sustainability and corporate responsibility.
Conclusion: The Quiet Revolution in Gas Compression
Reducing noise in gas compressors is more than just a matter of comfort—it’s about efficiency, safety, and profitability. Whether you’re dealing with workers’ health concerns, striving to comply with regulations, or simply trying to improve your operational efficiency, taking noise seriously is a win on multiple fronts.
By investing in noise reduction solutions, including sound enclosures, anti-vibration mounts, and advanced mufflers, you’re not just creating a quieter workspace. You’re improving your bottom line through reduced energy use, lower maintenance costs, and enhanced employee productivity. Plus, if you’re willing to explore cutting-edge technologies like Active Noise Control or Variable Speed Drives, you can take your noise management to a whole new level.
In the end, quieter compressors mean better, more sustainable operations—both for your employees and the environment. So, if you haven’t already, it’s time to start thinking about noise reduction in your gas compression systems. It’s not just a technical improvement—it’s a step toward a safer, more efficient, and more profitable future.
Final Thoughts
Noise reduction in gas compressors isn’t just a nice-to-have – it’s a practical step toward improving safety, efficiency, and overall workplace satisfaction. Whether you’re looking to build soundproof enclosures, use quieter compressor models, or simply make sure your systems are well-maintained, the options for reducing noise are numerous and effective.
Taking these steps to reduce compressor noise not only benefits the workers around the machine but also creates a quieter, more sustainable operation that can save you money in the long run. After all, quieter is always better when it comes to industrial equipment.